A couple weeks ago I went to a salvage yard and picked up an electric cooling fan from a 3.8L Taurus for $20. That fan upgrade is popular with the A-body crowd. After getting it home, it was apparent that it wasn't going to work in my situation. I'm using a different radiator then most people in this application and don't have much side to side adjustment. There must be a few differences that make this fan too thick. I'll have to run a solid fixed fan because I don't even have enough room for the thinnest clutch fan.
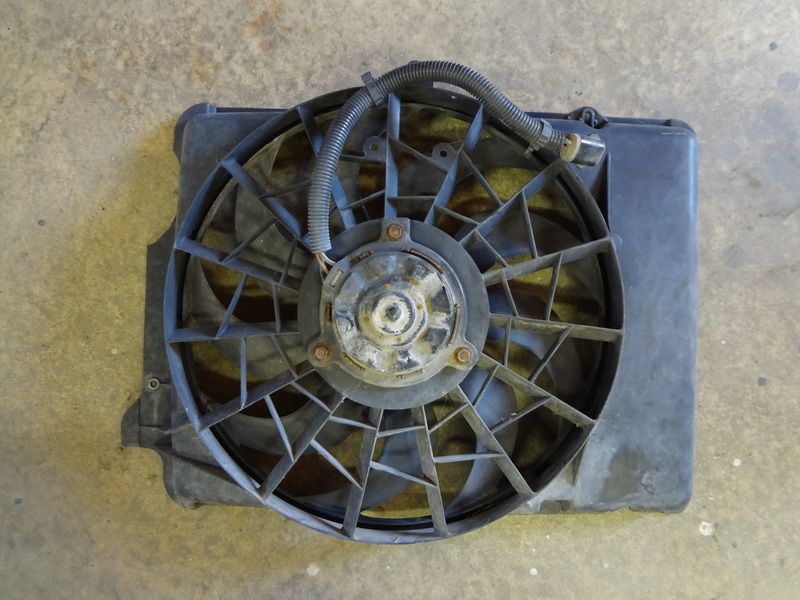
At 5" at it's thickest point, I don't have enough room to fit it in. Even trimming off the maximum from the back side, it's still way too thick.
That leads me to my latest project. There doesn't seem to be a fan shroud that fits the cc526 rad so I'm building one myself. Things got off to a rocky start but hopefully I can get the rest of it done without an hassles. A couple weeks ago I drew up a design and picked up a 26x21 sheet of 1/16" aluminum. I also picked up a scrap piece of aluminum so I could do some test bends on my brake. I questioned whether the scrap piece they gave me was aluminum and they said it was. When I tried to bend it, it wouldn't budge. At first I thought my brake was just too small. I talked to a metal fab company and they wanted $120 to bend the box for me. I didn't really want to spend that much so I looked closer at the scrap piece I tried to bend. It turns out that it was 1/16" stainless. No wonder my brake didn't like it.
The metal fab shop also asked what grade the aluminum was. They said if they tried bending 6061, it would crack at the bends. In order to bend 90 degree corners I'd need to use 3003 or possibly 5052. It turns out that I did have a piece of 6061 so I did some research on what it would take to bend it. It turns out it CAN be bent if you anneal it first. So, over the weekend I cut out the corners of the 6061 sheet and tried to anneal the areas that needed to be bent. My first bend went fine...no cracking. The second bend didn't go so well. I must not have gotten it hot enough and it cracked along the entire length of the bend.
On Monday, I went back where I bought the aluminum and told them what happened and that I needed a piece that could be bent. They looked puzzled and said, "You paid for 5052. I don't know why you ended up with a piece of 6061." So, they cut me a new piece of 5052 for free. Last night I got the new sheet bent with no cracking. 1/16" is still a little too much for my brake but I made it work. I'm going to cut a half circle notch in the top to clear the upper hose nipple.(I need to raise the shroud at least 1/2") and cut out the fan hole. Then, I'll need to get the corners welded. Here's what I have so far.
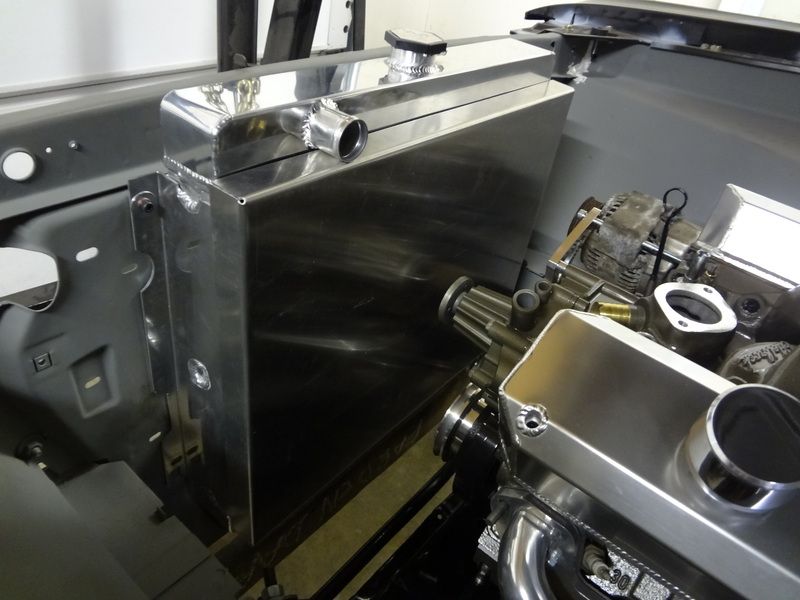
You can also see that I'm test fitting a denso alternator. The one that's on the engine right now is a 110amp unit from an Acura. It's pretty thick though and hits the valve cover. Since I won't be able to use an electric fan, I should be able to get away with a smaller 60amp denso.